Sistema de locomotora eléctrica sen conductor
A solución para o sistema de transporte por vía non tripulado
Na actualidade, o sistema nacional de transporte ferroviario subterráneo está dirixido e operado por persoal de correos no lugar.Cada tren necesita un condutor e un traballador da mina, e o proceso de localización, carga, condución e debuxo pódese completar coa súa cooperación mutua.Nesta situación, é fácil causar problemas como a baixa eficiencia de carga, a carga anormal e grandes perigos potenciais para a seguridade.O sistema de control do transporte ferroviario subterráneo orixinouse no estranxeiro na década de 1970.A mina de ferro subterránea de Kiruna en Suecia desenvolveu por primeira vez trens de control remoto sen fíos e tecnoloxía de comunicación sen fíos, e realizou con éxito o control remoto sen fíos dos trens subterráneos.Ao longo de tres anos de investigación e desenvolvemento independentes e experimentos de campo, Beijing Soly Technology Co., Ltd. por fin puxo en liña o sistema de circulación automática de trens o 7 de novembro de 2013 na mina de ferro Xingshan da empresa mineira Shougang.Ata agora estivo funcionando de forma estable.O sistema comprende con éxito que os traballadores poden traballar no centro de control terrestre en lugar de subterráneo, realiza o funcionamento automático do sistema de transporte ferroviario subterráneo e obtivo os seguintes logros:
Realizouse a operación automática do sistema de transporte ferroviario subterráneo;
En 2013, realizou o sistema de control remoto de trens eléctricos a 180 m na mina de ferro de Xingshan e gañou o primeiro premio de ciencia e tecnoloxía da minería metalúrxica;
Solicitou e obtivo a patente en 2014;
En maio de 2014, o proxecto aprobou o primeiro lote de aceptación de enxeñería de demostración da tecnoloxía de seguridade "catro lotes" da Administración Estatal de Xestión e Control de Seguridade.
Solución
A solución de operación automática do sistema de transporte ferroviario subterráneo desenvolvido por Beijing Soly Technology Co., Ltd. solicitouse e obtivo a patente e foi recoñecida conforme polos departamentos nacionais relevantes, o que é suficiente para demostrar que este sistema combina con éxito sistemas de comunicación. , sistemas de automatización, sistemas de rede, sistemas mecánicos, sistema eléctrico, sistema de control remoto e sistema de sinalización.O mando de operación do tren realízase coa ruta de condución óptima e o método de contabilidade custo-beneficio, o que mellora significativamente a taxa de utilización, a capacidade e a seguridade da liña ferroviaria.O posicionamento preciso do tren conséguese mediante odómetros, correctores de posicionamento e velocímetros.O sistema de control de trens (SLJC) e o sistema pechado centralizado de sinal baseado no sistema de comunicación sen fíos realizan o funcionamento totalmente automático do transporte ferroviario subterráneo.O sistema integrado co sistema de transporte orixinal na mina, ten expansibilidade, que satisface as necesidades de diferentes clientes e é adecuado para minas subterráneas con transporte ferroviario.
Composición do sistema
O sistema consiste na unidade de despacho de trens e de dosificación de mineral (sistema dixital de distribución de mineral, sistema de despacho de trens), unidade de tren (sistema de transporte de trens subterráneos, sistema de protección de trens automático), unidade de operación (sistema pechado centralizado de sinal subterráneo, sistema de consola de operación, comunicación sen fíos). sistema), unidade de carga de mineral (sistema de carga remota por canal, sistema de seguimento de vídeo de carga remota por canal) e unidade de descarga (sistema de estación de descarga subterránea automática e sistema de limpeza automática).
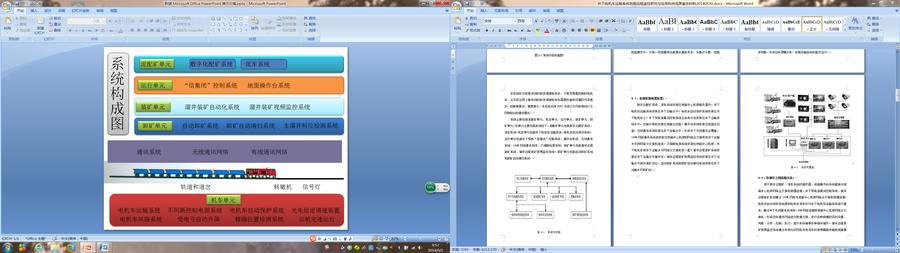
Figura 1 Diagrama de composición do sistema
Unidade de despacho de trens e de dosificación de mineral
Establecer un plan de proporción óptimo de mineral centrado no canal principal.Desde a estación de descarga, seguindo o principio de calidade de produción estable, segundo as reservas de mineral e a calidade xeolóxica de cada canal na zona mineira, o sistema envía dixitalmente trens e mestura minerais;segundo o plan de proporción óptimo do mineral, o sistema organiza directamente o plan de produción, determina a secuencia de extracción do mineral e a cantidade de cada canal e determina os intervalos de funcionamento e a ruta dos trens.
Nivel 1: proporción de mineral no taboleiro, é dicir, o proceso de proporción de mineral que comeza a partir dos raspadores que escavan minerais e despois vertien minerais aos toboganes.
Nivel 2: proporción do canal principal, é dicir, o proceso de dosificación do mineral desde os trens que cargan minerais de cada canal e despois descargan minerais ó canal principal.
Segundo o plan de produción elaborado polo plan de proporción de mineral de nivel 2, o sistema pechado centralizado de sinal dirixe o intervalo de operación e os puntos de carga dos trens.Os trens teledirixidos completan as tarefas de produción no nivel de transporte principal segundo a ruta de condución e as instrucións dadas polo sistema pechado centralizado de sinal.
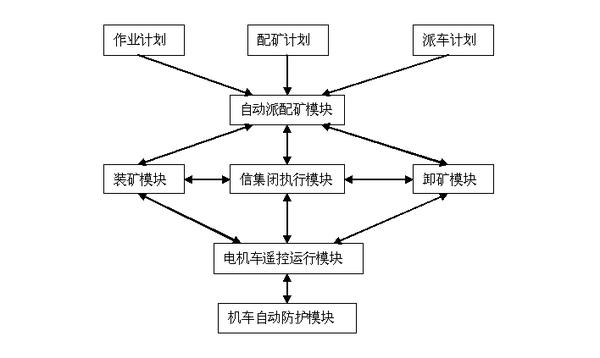
Figura 2. Diagrama de cadros do sistema de despacho de trens e dosificación de mineral
Unidade de tren
A unidade de tren inclúe un sistema de transporte de trens subterráneos e un sistema automático de protección do tren.Instale o sistema de control industrial automático no tren, que pode comunicarse co sistema de control da consola na sala de control a través de redes sen fíos e con fíos, aceptar varias instrucións do sistema de control da consola e enviar a información de operación do tren ao control da consola. sistema.Unha cámara de rede está instalada na parte dianteira do tren eléctrico que se comunica coa sala de control terrestre a través dunha rede sen fíos, para realizar un seguimento remoto de vídeo das condicións do ferrocarril.
Unidade de operación
A través da integración do sistema pechado centralizado de sinal, o sistema de mando do tren, o sistema de detección de posición precisa, o sistema de transmisión de comunicación sen fíos, o sistema de vídeo e o sistema de consola terrestre, o sistema realiza o funcionamento do tren eléctrico subterráneo mediante control remoto no chan.
Operación do control remoto terrestre:o operador do tren na sala de control emite unha aplicación de carga de mineral, o despachador envía instrucións de carga de mineral de acordo coa tarefa de produción e o sistema de pechado centralizado de sinal cambia automaticamente os semáforos segundo as condicións da liña despois de recibir a instrución e dirixe o tren. ao tobogán designado para cargar.O operador do tren controla remotamente o tren para que corra ata a posición designada a través do asa.O sistema ten a función de cruceiro de velocidade constante e o operador pode establecer diferentes velocidades a diferentes intervalos para reducir a carga de traballo do operador.Despois de chegar ao canal de destino, o operador realiza a extracción de mineral de forma remota e move o tren á posición correcta, asegúrese de que a cantidade de mineral cargada cumpra os requisitos do proceso;despois de rematar a carga de mineral, solicitar a descarga e, despois de recibir a solicitude, o sistema centralizado de sinal pechado xulga automaticamente os ferrocarrís e ordena o tren ata a estación de descarga para descargar minerais, completando un ciclo de carga e descarga.
Funcionamento totalmente automático:Segundo a información de mando do sistema de distribución e distribución de mineral dixital, o sistema pechado centralizado de sinal responde automaticamente, comanda e controla as luces de sinal e cambia as máquinas para formar a ruta de execución desde a estación de descarga ata o punto de carga e desde o punto de carga ata o punto de carga. estación de descarga.O tren funciona de forma totalmente automática segundo a información e os comandos completos do sistema de distribución de mineral e despacho de trens e do sistema pechado centralizado de sinal.En marcha, en función do sistema de posicionamento preciso do tren, determínase a posición específica do tren e o pantógrafo elévase e baixa automaticamente segundo a posición específica do tren, e o tren corre automaticamente a velocidades fixas en diferentes intervalos.
Unidade de carga
A través das imaxes de vídeo, o operador opera o sistema de control de carga de mineral para realizar a carga de mineral de forma remota na sala de control terrestre.
Cando o tren chega ao canal de carga, o operador selecciona e confirma o canal necesario a través da pantalla do ordenador de nivel superior, para conectar a relación entre o canal controlado e o sistema de control do chan, e emite comandos para controlar o canal seleccionado.Ao cambiar a pantalla de vixilancia de vídeo de cada alimentador, o alimentador vibratorio e o tren funcionan de forma unificada e coordinada, para completar o proceso de carga remota.
Unidade de descarga
A través do sistema automático de descarga e limpeza, os trens completan a operación de descarga automática.Cando o tren entra na estación de descarga, o sistema de control automático de operación controla a velocidade do tren para garantir que o tren pasa polo dispositivo de descarga de ferrocarril curvo a unha velocidade constante para completar o proceso de descarga automática.Ao descargar, o proceso de limpeza tamén remata automaticamente.
Funcións
Dar conta de que ninguén traballa no proceso de transporte ferroviario subterráneo.
Realice o funcionamento automático do tren e mellora a eficiencia do funcionamento do sistema.
Efecto e beneficio económico
Efectos
(1) Eliminar os riscos potenciais para a seguridade e facer que o tren circule máis estandarizado, eficiente e estable;
(2) Mellorar o nivel de transporte, automatización da produción e informatización e promover o progreso e a revolución da xestión;
(3) Mellorar o ambiente de traballo e mellorar a eficiencia da produción do transporte.
Beneficios económicos
(1) A través do deseño optimizado, conseguir unha proporción óptima do mineral, reducir o número de trens e o custo de investimento;
(2) Reducir o custo dos recursos humanos;
(3) Mellorar a eficiencia e os beneficios do transporte;
(4) Para garantir unha calidade estable do mineral;
(5) Reducir o consumo de enerxía dos trens.